Faulty mechanical and thermal style steam traps can have significant financial implications for industrial processes that rely on steam systems. Steam traps are essential components that help remove condensate from steam systems while preventing the loss of steam. When these traps malfunction or fail, several financial consequences can arise.
1. Faulty Mechanical Steam Traps Leads To Energy Loss
Faulty steam traps can result in the loss of valuable steam, leading to increased energy consumption and higher utility bills. Steam is often generated by burning fuels or using electricity, both of which come at a cost. The continuous loss of steam due to faulty traps means that more energy must be expended to maintain the desired steam pressure and temperature, resulting in increased operating costs. It only takes a small amount of faulty steam traps in your facility to be wasting hundreds of thousands of dollars.
2. Malfunctioning Steam Traps Reduces Efficiency
Steam traps play a crucial role in maintaining the efficiency of steam systems. Malfunctioning traps can cause inadequate condensate removal, leading to reduced heat transfer efficiency. When condensate accumulates in the steam lines or heat exchangers, it acts as an insulating barrier, impeding the transfer of heat and reducing overall system performance. Reduced efficiency translates to higher energy ency consumption and longer processing times, ultimately impacting productivity and increasing operational expenses.
3. Trap Failure Creates Equipment Damage
Steam traps are responsible for removing water and condensate from steam lines, preventing water hammer, and protecting downstream equipment from damage. When faulty traps fail to remove condensate effectively, water can accumulate in pipes, valves, and other steam-driven equipment. Water hammer, caused by the rapid condensation of steam, can occur, leading to pipe ruptures, valve failures, and other mechanical damage. Repairing or replacing damaged equipment can be costly and cause production delays.
4. Increased Maintenance and Repair Costs
Detecting and rectifying faulty steam traps require regular inspections and maintenance. Troubleshooting faulty traps, repairing or replacing them, and restoring the steam system’s proper functioning can involve significant labor costs, material expenses, and downtime for production. Additionally, if faulty traps are not promptly identified and repaired, the overall wear and tear on the steam system may increase, necessitating more frequent maintenance and repair interventions.
5. Costly Environmental Impact
Inefficient steam systems resulting from faulty traps contribute to increased carbon emissions and environmental impact. The excess energy consumption required to compensate for the loss of steam contributes to a higher carbon footprint. In an era of increasing environmental consciousness and stricter regulations, such inefficiencies may lead to additional costs in the form of carbon taxes or penalties.
Mitigate These Costly Issues Buy Investing In Delta Steam Traps
To mitigate the financial impact of faulty mechanical and thermal steam traps, customers are choosing Delta Steam Traps, a permanent solution for this perpetual problem. The Delta Steam Trap operates without any moving parts and has proven over the last 25 years to outperform mechanical and thermal style steam traps.
We can look in your facility where you could be wasting hundreds of thousands of dollars a year on wasted steam through faulty steam traps. Let’s plan on replacing those steam traps with a permanent steam trap solution, the Delta Venturi Steam Trap.
See from our Delta Steam Trap expert, Greg Bayerl, on the financial disadvantages of mechanical and thermostatic steam traps on our YouTube channel.
Delta Steam Traps | Frequently Asked Questions→
How Delta Steam Traps Can Work In Your University→
Interested in a demo and complimentary steam trap survey?
About the Author
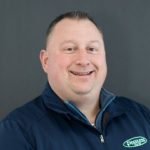
Greg Bayerl
Business Development – Process/MRO
Greg Bayerl is a Business Development Representative based in Buffalo, NY. He has been with the Peerless team for 6 years specializing in the MRO market.